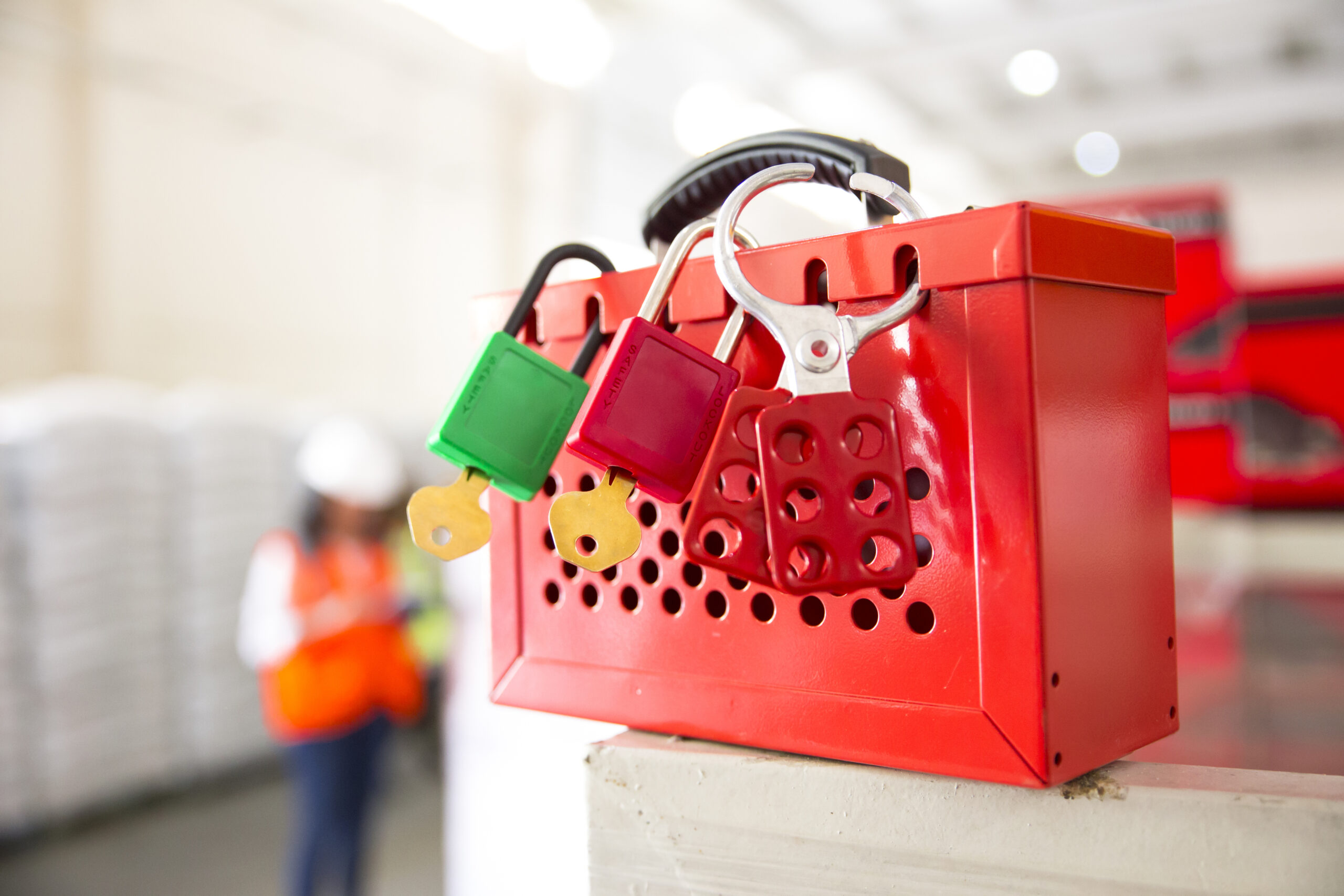
lockout tagout
A prominent sausage manufacturer has recently come under intense scrutiny for repeated safety violations related to Lockout/Tagout (LOTO) procedures. The Occupational Safety and Health Administration (OSHA) cited the company for failing to adhere to essential safety protocols designed to protect workers from hazardous energy during maintenance activities. This incident underscores the critical importance of LOTO procedures in preventing workplace injuries and ensuring employee safety.
Summary of the Incident
The sausage manufacturer, already familiar with OSHA’s enforcement actions, was found to have multiple repeat violations concerning its Lockout/Tagout procedures. These violations included failing to properly de-energize equipment before maintenance, inadequate employee training on LOTO practices, and not conducting periodic inspections of energy control procedures. OSHA’s investigation revealed that these lapses exposed workers to serious risks of injury from unexpected machinery startups.
Specifically, OSHA identified instances where the company did not ensure that machinery was adequately powered down before maintenance tasks were performed. This led to situations where workers were at risk of severe injury from sudden machinery movements. Moreover, the investigation revealed that the company had not provided comprehensive training for its employees on the proper use of LOTO devices and procedures. As a result, workers were not adequately informed about the dangers they faced or the correct methods for ensuring their safety.
Such repeated violations indicate a systemic issue within the company’s safety management practices. This not only puts employees at risk but also highlights the need for stringent adherence to LOTO protocols. Proper implementation of these procedures is not just a regulatory requirement but a fundamental aspect of protecting workers’ lives and well-being.
The Importance of Lockout/Tagout Compliance
Compliance with LOTO procedures is not merely a regulatory requirement but a crucial practice for ensuring workplace safety. According to OSHA, failure to implement proper LOTO procedures is one of the top violations cited each year, often resulting in severe injuries or fatalities. The primary goal of LOTO is to protect workers from the unexpected energization or release of stored energy, which can cause serious harm.
When companies neglect these procedures, the consequences can be dire. Employees may face severe injuries such as amputations, fractures, electrocutions, and even death. Moreover, the financial impact on the company can be substantial, including fines, increased insurance premiums, and potential lawsuits. Beyond these tangible costs, the damage to a company’s reputation can be long-lasting, affecting its ability to attract and retain talent.
Upcoming Lockout/Tagout Training Class by NASP
To address the critical need for proper Lockout/Tagout training, the National Association of Safety Professionals (NASP) is offering a comprehensive live training class on LOTO procedures. This course is designed to equip safety professionals, maintenance workers, and supervisors with the knowledge and skills necessary to implement and manage effective LOTO programs in their workplaces.
Course Details:
- Title: Lockout Tagout Train-The-Trainer Classroom Course
- Date: July 18-19, 2024
- Format: Live, in-person training
- Register here
Participants in this training will learn:
- The importance of LOTO procedures and regulatory requirements.
- How to develop and implement a comprehensive LOTO program.
- Techniques for identifying and controlling hazardous energy sources.
- Best practices for training employees and conducting periodic inspections.
- Case studies of LOTO failures and successes to illustrate real-world applications.
By attending this training, participants will gain valuable insights and practical skills to enhance workplace safety and ensure compliance with OSHA standards. This course will cover detailed LOTO procedures, risk assessment strategies, and the latest regulatory updates to help organizations maintain a safe working environment.
The recent violations by the sausage manufacturer serve as a stark reminder of the importance of rigorous Lockout/Tagout procedures. Ensuring compliance with these safety protocols is essential for protecting workers and preventing tragic accidents. Investing in proper training, such as the upcoming NASP LOTO training class, is a crucial step toward achieving a safer work environment. Let’s prioritize safety by adhering to LOTO procedures, training employees effectively, and continuously improving our safety practices. By doing so, we can safeguard the well-being of our workforce and uphold the highest standards of workplace safety.