Trenching and excavation safety
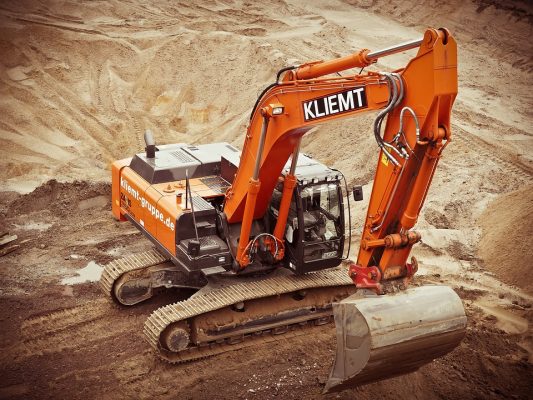
Proper protective systems, competent person key to incident prevention
George Kennedy can recall multiple incidents involving unprotected workers and trench cave-ins. Unfortunately, some of those stories have tragic endings.
One worker was killed in a collapse after removing a trench shield to retrieve a shovel.
Another worker died after returning to an unprotected trench to grab a pack of cigarettes that had fallen from his pocket and a cave-in occurred.
Kennedy, vice president of safety for the National Utility Contractors Association, is among those working to raise trench safety awareness.
“They just should not take the chance of going into an unprotected trench for any reason for any period of time,” Kennedy said. “Even 30 seconds, a minute. That’s all it takes. Cave-ins happen in a fraction of a second. You turn around and it’s on you.”
Staying protected
OSHA defines an excavation as “any man-made cut, cavity, trench or depression in the earth’s surface formed by earth removal.” A trench is “a narrow underground excavation that is deeper than it is wide, and is no wider than 15 feet.” The agency points out that 1 cubic yard of soil can weigh up to 3,000 pounds – approximately the weight of a small car.
The fatality rate for excavation work is 112 percent higher than the rate for general construction, OSHA data shows. The agency lists “employee injury from collapse” as the primary hazard of excavation work and includes “no protective system” among the leading causes of worker injuries.
According to OSHA, 23 workers were killed in trench collapses in 2016, surpassing the combined total from 2014 and 2015. No matter the nature of the work or depth of the trench, excavations are unstable, experts note.
“Employers need to recognize that any excavation has the potential for exposure to serious injury or fatality, and have systems in place to verify that precautions are specifically identified and carried out consistently,” said Larry R. Russell, principal consultant at DEKRA Organizational Safety & Reliability.
The OSHA standard for trenching and excavation – 29 CFR 1926.650-652, Subpart P – requires protective systems for trenches that are 5 feet or deeper, unless the excavation occurs in stable rock. A registered professional engineer must design protective systems for trenches that are at least 20 feet deep or approve tabulated data prepared for the system.
In July, OSHA unveiled a free sticker intended to remind workers of the three primary protective systems:
- Sloping (or benching). Cutting back the trench wall at an angle inclined away from the excavation.
- Shoring. Installing aluminum hydraulics or other types of supports to prevent cave-ins.
- Shielding. Using trench boxes or other supports to prevent cave-ins.
Joe Turner, director of engineering, research and product development at National Trench Safety, said serious injuries and fatalities in excavation work often result from one of two circumstances. “Either where there’s no shoring at all,” he said, “or where the contractor misapplies the shoring system – doesn’t do it properly, doesn’t do a job hazard analysis before they begin the shoring, that sort of thing.”
As work conditions dictate
Chris Cain, executive director of the Center for Construction Research and Training (also known as CPWR), stressed that excavations are dug in response to the needs of the worksite, and protective systems follow the same logic.
When choosing protective systems, a safety officer or competent person must consider various factors, including soil classification, depth of cut, water content of soil, weather- or climate-driven changes, surcharge loads, and other nearby operations. Not every protective system is suitable for each type of soil. Employers should ensure workers are trained on trenching hazards and develop an emergency action plan.
“We’ve made a lot of progress,” said Ron Chilton, president of the North American Excavation Shoring Association, “but we’re still a dangerous profession. … The jobs are getting bigger and the excavation is getting larger and deeper and more complex.”
OSHA requires a safe means of access or egress – such as ladders, steps and ramps – to be located within 25 feet of all workers for excavations 4 feet or deeper. Workers should keep heavy equipment away from trench edges, keep surcharge loads at least 2 feet from trench edges and never work under raised loads.
Following these guidelines helps limit struck-by incidents, Kennedy said. Wearing high-visibility clothing such as shirts, jackets, sweaters or vests can contribute to mitigating yet another hazard for workers in excavation: worker visibility.
“The equipment swings around and the operator doesn’t know the [person] is there,” Kennedy said. “And lots of times, it’s due to the fact that they’re hard to see sometimes and they don’t make themselves visible to the operator.”
‘Extremely important to have a competent person’
Preplanning is paramount in excavation work. The designated competent person leading the operation takes a central role by mastering OSHA regulations and recognizing existing and potential hazards.
As required by Subpart P, the competent person must inspect trenches before work starts, as well as after events in which conditions change or hazards increase, such as rainstorms.
“Inspecting is a big deal for trenches, because the conditions change from day to day if a trench is open for a long period of time, or even for more than one day,” Cain said, adding that atmospheric hazards also might arise from work and could resemble those found in confined spaces.
A job near an underground natural gas line, for example, would warrant air sampling. Employers should call 811 before digging so utility workers can come out and mark the locations of underground lines.
Further, Cain said, crews working near old landfills should be mindful of a possible exposure to methane gas or hydrogen sulfide – an odiferous, toxic gas.
Russell recommends a competent person consult OSHA’s technical manual on hazard recognition in trenching and shoring.
Questions a competent person should ask during a site assessment include:
- Is the cut, cavity or depression a trench or an excavation? Is it more than 4 feet deep? Does it contain water?
- Are there adequate means of access and egress? Are there surface encumbrances or exposures to vehicular traffic? Are adjacent structures stabilized?
- Is equipment operating near the trench or excavation? Does the equipment have warning systems?
- Does the trenching or excavation work require sloping, shoring or shielding? If shielding is used, does the shield extend at least 18 inches above the surrounding area if it is sloped toward the excavation? Is the depth of the cut more than 2 feet below the bottom of the shield?
- Is emergency rescue equipment required?
- Is there documentation of the minimum daily excavation inspection?
“It’s extremely important to have a competent person on the job,” Kennedy said, “because they’re going to make sure that they are using their protective system, that it is set up properly. And they’re making sure workers don’t take chances, ladders are set up, [excavated soil] piles are set back at least 2 feet from the edge of the excavation. All the things that go along with making sure the trench is safe before a worker goes into it.”
Said Turner: “If that process is followed and it happens, it prevents workers from getting trapped and having cave-ins. If they don’t follow that process, if they don’t provide shoring, this is where you read about most of the deaths in excavations.”
Talking it over
Subpart P states that trench backfilling “shall progress together with the removal of support systems from excavations” as work nears its completion.
Once backfilling is finished, Cain recommends evaluating work during a post-job discussion.
“After a significant job with significant safety risks, it’s always important to do some kind of look back and make sure that things went right,” Cain said. “And if things went wrong or there was evidence that things could be going wrong, just do a debrief and figure out with the crew, the competent person, the foreman and whoever the management is onsite. Ask, ‘How did it go? Was anything unexpected encountered? What could we have done to avoid that?’
“That type of thing is always a good activity to do. It could be a five-minute discussion right after a particularly hazardous job. It could actually make a difference in the next job or the job after that.”
Click here to view our Construction CSM class
Purchase Our Certified Safety Manager: Construction Course Online