Troubleshooting 4 Common Gas Detection Issues
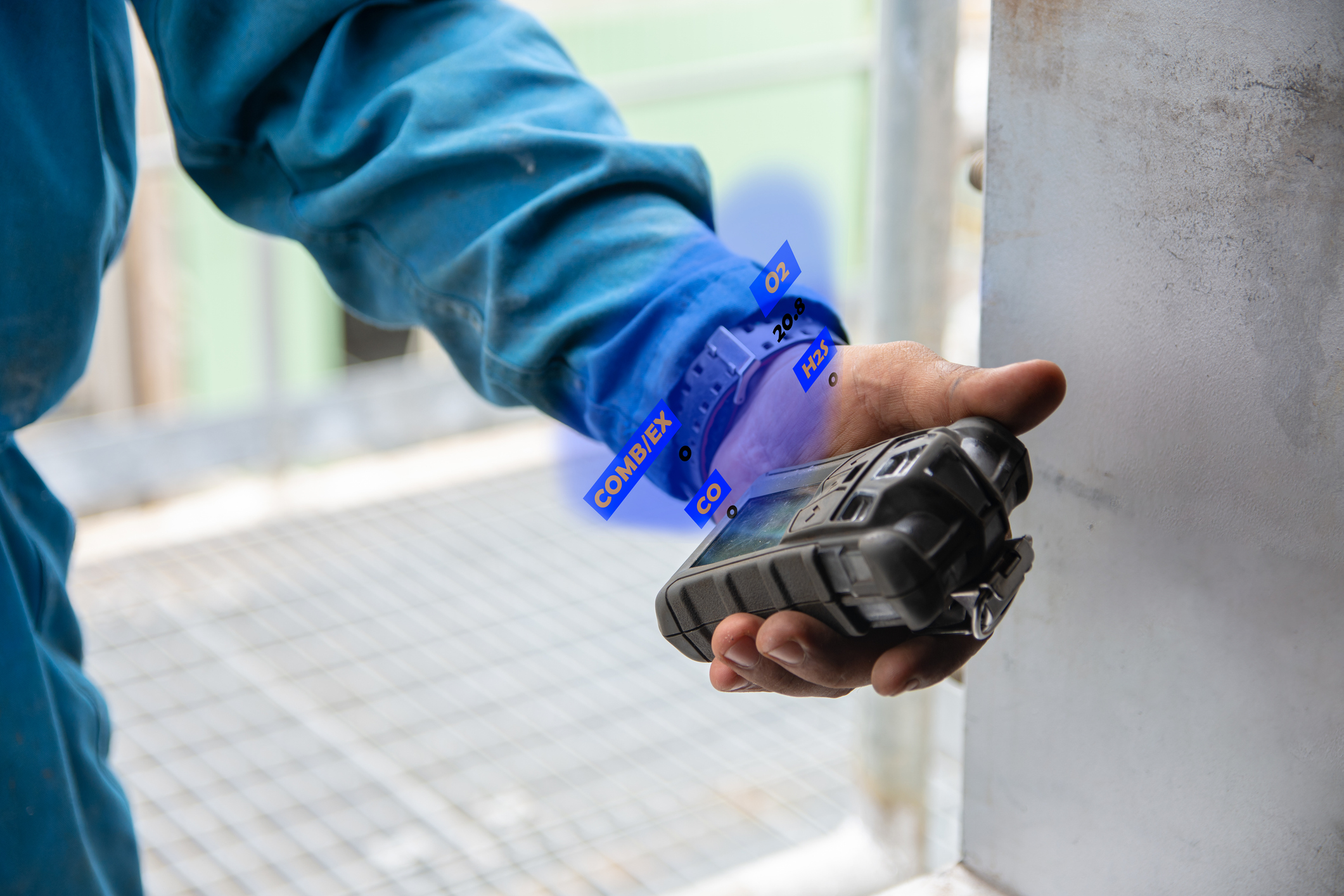
Gas detection has come a long way since canaries warned miners of toxic gases in the 19th century. Today’s advanced sensors, including infrared and electrochemical types, keep workers safe in industries like oil, gas, and wastewater treatment. The global gas detection market, valued at $1.85 billion, highlights the critical role of these devices in worker safety. However, even the most advanced gas detectors can face issues, and understanding how to troubleshoot these problems is essential for maintaining a safe work environment. Here, NASP explores four common gas detector issues and offers practical solutions.
1. Gas Detector Won’t Turn On
Power issues are common but manageable with these steps:
- Check the Battery: Replace or recharge the battery if needed. Examine the compartment for leaks, corrosion, or damage, and ensure the temperature is suitable for device operation.
- Inspect Power Contacts: Clear dust or corrosion from the battery contacts or power connectors with a dry cloth. For fixed detectors, check the power cable for damage and verify voltage at the terminal block.
- Software and Firmware Updates: Bugs can interfere with powering up, so updating firmware may solve the issue.
If the device remains unresponsive, contact the manufacturer, as service or parts replacement may be necessary.
2. Gas Detector Won’t Calibrate
Calibration is critical to ensuring accurate readings. Failing calibration may endanger worker safety by providing inaccurate data.
- Expired Sensors: Sensors typically last two to three years. If calibration fails, check whether a sensor replacement is needed.
- Incorrect Calibration Gas: Ensure you’re using the correct gas type and concentration, and that it’s within the expiration date, as expired gas can lead to inaccurate readings.
- Environmental Conditions: High humidity or extreme temperatures can impact calibration. Calibrate in a controlled environment, and always start with a fully charged device.
Routine bump testing before each use and calibrating at least every six months is recommended to maintain accuracy.
3. Sensor Error and Replacement
As sensors age, they lose sensitivity, leading to errors or false readings.
- Sensor Lifespan: Check the user manual for each sensor’s expected life. Replacement may be needed for sensors nearing their end of life.
- Identify the Error Code: Refer to the manual for error code troubleshooting guidance.
- Sensor Maintenance: Regularly clean the sensor housing to prevent dirt buildup from interfering with readings. Avoid abrasive cleaning tools.
- Cross-Interference: Electromagnetic interference (EMI) from devices like cell towers can lead to false readings. Sensor stabilization in ambient air, usually between 30 minutes to three hours, helps ensure reliable data.
4. Cross-Sensitivity Issues
Cross-sensitivity occurs when a sensor detects non-target gases, which can lead to false alarms.
- Use Filtered Sensors: Filters can block non-target gases and reduce cross-sensitivity. Consider upgrading to filtered sensors if cross-sensitivity is frequent.
- Regular Calibration: Calibrating regularly can help the detector adjust to environmental changes, reducing cross-sensitivity.
- Proper Ventilation: Adequate airflow in work areas minimizes the chance of cross-sensitivity by dispersing non-target gases.
Manufacturers often provide cross-sensitivity charts, which are helpful resources for workers to carry on-site.
Importance of Maintenance
Maintaining gas detectors extends their lifespan and ensures they function reliably. Here are NASP’s best practices:
- Routine Sensor Testing: Regular bump testing verifies sensor responsiveness. Many detectors have docking stations that automate testing and reminders.
- Document Maintenance: Detailed records of maintenance, testing, and calibrations are invaluable. Detectors with data-logging features can simplify this process.
- Proper Storage: Store detectors in dry, controlled environments to protect sensitive components.
Gas detectors, though robust, need regular care. Workers should check their detectors before each use, just as they do other safety equipment.
Embracing Connectivity for Enhanced Safety
Connected technology allows gas detectors to link with third-party apps, making safety monitoring accessible and affordable. These advancements give managers real-time insights for early troubleshooting and proactive maintenance, fostering safer workplaces. By equipping workers with the skills to maintain and troubleshoot gas detectors, NASP ensures that everyone can work safely and return home at the end of the day.