How to Create a Safety Culture in the Construction Industry
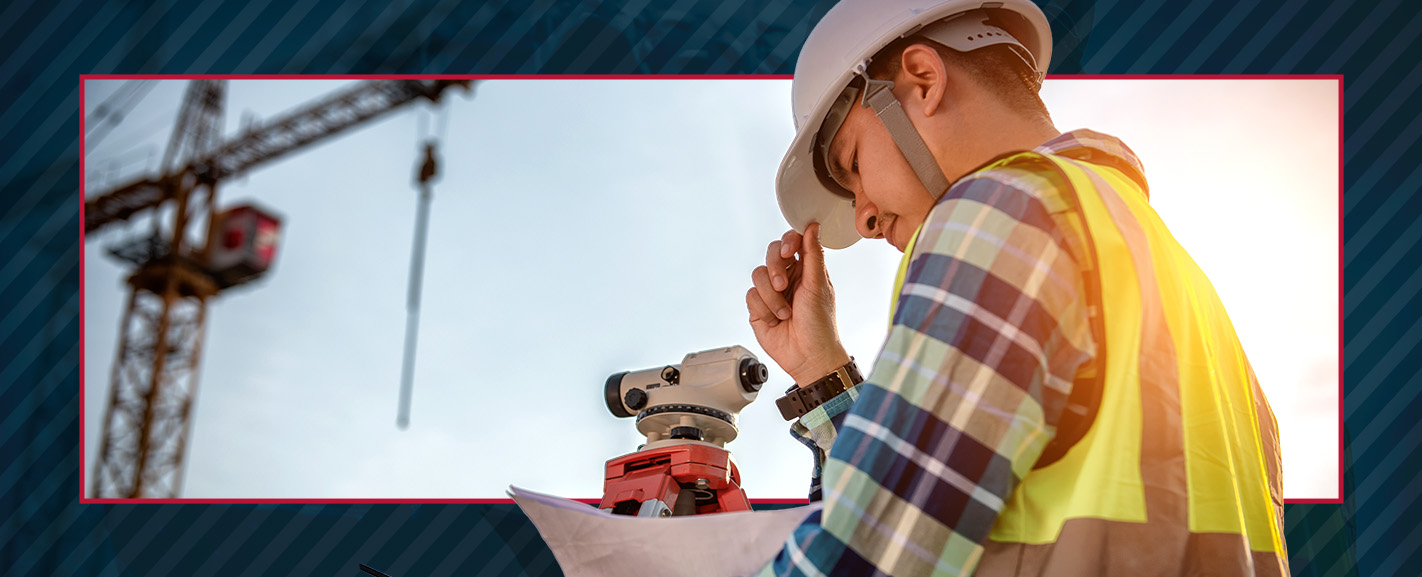
Fostering a safe workplace can help construction companies promote a positive working environment for employees. Most importantly, it prevents injuries and fatal accidents. You can follow several tips to keep your workers safe and protect your business’s reputation.
The Current Safety Situation in Construction
The importance of learning how to create a safety culture in construction lies in the statistics of dangers in this field. It’s no secret that it’s a risky industry to work in. However, most accidents, injuries, and fatalities can be prevented with an effectively protected work environment.
The National Institute for Occupational Safety and Health (NIOSH) describes construction work as one of the most dangerous fields. It points out that between 2015 and 2017, small companies with fewer than 20 employees were responsible for 75% of fatal falls. Due to the following factors, Hispanic and female workers are at increased risk of injuries compared to their United States-born counterparts:
- Lack of training material in Spanish
- Limited safety programs in small construction businesses
- Fewer personal protective equipment (PPE) or lack of PPE that fits different sizes and sexes
Additionally, the U.S. Bureau of Labor Statistics highlights that the construction industry accounted for nearly half of all fatal slips, trips, and falls in 2022. These fatal injuries can significantly affect a company’s reputation and productivity. They also create financial implications like legal fees, higher insurance premiums, and Occupational Safety and Health Administration (OSHA) fines.
The Top Tips to Create a Culture of Safety in Construction
If you are wondering how to create a positive construction safety culture, it starts with building a positive attitude toward safety. Employees need to know that the company values and prioritizes their health and safety.
Here are some of the best tips to highlight the importance of safety in construction. They’ll help create a space where everyone works to identify hazards, provide solutions, and ensure a safe work environment.
Prioritize Mental Health
Mental health plays a bigger role in safety than most companies know. Employee well-being and safety at the workplace are linked, especially in the construction field. Studies reveal that anxiety and depressive disorders run rife among laborers. It’s one of the major industry groups with the highest suicide rates among employees.
The long hours and strenuous labor can also take a toll on employees’ mental health. Working in an environment that doesn’t prioritize safety can also worsen some symptoms of anxiety. A healthy mind can help workers remain alert, spot and avoid potential hazards, and promote work safety. So, what can employers do? Here are four tips to improve mental health in the workplace and create a positive environment:
1. Promote a Healthy Work-Life Balance
Construction is hard work, but it doesn’t have to be unrealistic. Manage the workload so that individuals have a reasonable amount of work. They should be able to complete tasks without pushing themselves to exhaustion. Make time for employees to socialize and create connections in the workplace.
Ensure that employees are taking regular breaks and aren’t working through their breaks to catch up on work. If you can, provide a refreshment station for workers to stay hydrated and catch up with others on their breaks. Create awareness about the dangers of burnout and encourage staff to enjoy their days off. Stick to clock-in and clock-out times so they can build a healthy work-life balance.
2. Provide Mental Health Programs and Resources
One of the best ways to create a great construction safety culture is to learn how to provide a space for workers to manage stress. Create programs or counseling services for employees to work through their negative experiences.
Ensure that counseling services or resources are available in the primary languages your workers speak. Companies could also host monthly mental health workshops, helping equip staff with tools to handle stressful conditions.
Implement policies that aim to reduce mental health stigma. Promote an environment where asking for help and sharing feelings is accepted and welcomed.
3. Create Mentorship and Support Systems
A mentorship or partner program can help workers support each other and watch out for potential hazards. Peer support groups are also an excellent way to create a welcoming environment where employees feel a sense of belonging.
4. Implement Safety Committees
Safety committees comprised of staff from superintendents to field workers can help ensure that safety practices are being implemented and followed. They can meet regularly to discuss the processes and practices involved in on-site and off-site work.
Committees can play an integral role in reviewing safety policy documents and ensuring everyone is up-to-date on the latest industry practices. Safety managers should talk to workers on-site about what can improve conditions.
The committee should include a range of workers. They can use their varying expertise to prepare for potential emergencies they may face in construction. One of the safety committee’s main roles is to develop a robust emergency plan and raise awareness about potential work-related hazards.
Organize Regular Safety Training
Regular training is the best way to create a culture of safety in construction because it focuses on following safety guidelines. Providing your employees with ongoing training helps keep them updated with new changes in the industry.
The aging workforce typically has extensive knowledge of accident prevention. However, staff members can become overly confident and develop potentially dangerous habits. Ongoing training reminds them of the safe way of doing things. It encourages other workers to follow trainers’ advice rather than that of other laborers.
Of course, implementing safety tasks routinely can become overwhelming for workers to remember. Companies can make this easier and improve safety in the workplace by implementing these solutions:
1. Digitize the Safety Process
Eliminate pen-and-paper methods for safety processes. They can make things more stressful and complex than they need to be. Mobile solutions are an excellent way to streamline the safety recording process and make it less overwhelming for workers.
Incorporate a user-friendly mobile app with an intuitive and engaging interface. Remember, the goal of the app is to speed up those time-consuming safety tasks. It should be simple to use and navigate, even for workers who are not tech-savvy. It can also be used to automate tedious and routine tasks.
2. Accept Regular Feedback
Make a habit of getting feedback from workers on new procedures and tools. This can help your company make improvements and boost efficiency. Employees will also be able to highlight potential hazards in certain processes that will revamp safety measures.
Create Preconstruction Safety Planning Outlines
In the planning stage for every project, creating a preconstruction plan can promote a safe job site. It protects workers from injuries that could be prevented by awareness of potential threats and plans to avoid them. Five major steps go into creating an effective plan:
1. Identify the Potential Hazards
Pinpoint the hazards that might arise during each construction phase. This can be done via risk assessments, inspections, or consulting with stakeholders or on-site workers. Potential hazards include:
- Electrical shocks
- Explosions
- Fires
- Equipment malfunctions
- Noise
- Traffic
- Falling objects
- Chemicals
2. Assess the Risks
Think of the possible hazards that may harm workers, people nearby, or the environment. Categorize each potential risk as low, medium, or high based on the extent of damage it may cause and the possibility of it happening.
Falls from elevation are one of the most important risks to assess because they’re the leading cause of fatalities in construction. Locate all the areas where they’re most likely to occur. These might include areas with a lot of traffic, staircases, and wet or slippery areas. Afterward, you can implement engineering and administrative controls targeted at preventing falls that could cause injury or death.
Assessing the risks can help promote a culture of safety regarding falls and create more awareness of potential risks.
3. Create Control Measures
Implement control measures to minimize risks as much as possible. Think about them thoroughly, as they play a vital role in preventing harm from hazards. Here are some examples:
- Wearing PPE
- Using warning signs and lights
- Eliminating certain tasks
- Substituting hazardous tasks with less-involved options
Keep a record of all the control measures so you can determine their efficiency and apply them in similar circumstances in the future.
4. Communicate the Plan
Once a plan is established, the superiors must communicate it to the workers and contractors. Ensure that the plan is released in languages spoken by the on-site employees. That way, everyone knows which hazards to look out for and how to deal with them.
You can use many methods to get the message across, such as safety briefings, multilingual posters, or toolbox talks.
5. Update the Outlines
When the conditions or scope of a project change, you need to review and update the outlines. This step keeps your plans fresh and ensures they’re on par with the current standards and regulations. Some methods to update it include inspections, worker feedback, and looking at previous incident reports.
Emphasize the Importance of Inspection Reports
Inspection reports should always be taken seriously. They have the potential to mitigate risks and prevent injuries, illnesses, and fatal accidents. Emphasizing their importance ensures teams are prepared and helps managers know where to take corrective actions.
Conducting effective safety inspections helps with the following areas:
- Legal compliance: Companies can rectify issues that may have legal consequences and hurt their reputation and finances.
- Safety culture: Taking inspection reports seriously shows that your company prioritizes a culture of safety.
- Identifying hazards: Inspection reports can help identify concerns that committees may have missed.
Reward Good Safety Responses
Creating a culture of safety in construction is all about promoting proactive steps and communication. Every worker can play a part in preventing injuries. They should be encouraged to speak freely about the problems they observe.
It’s crucial to recognize and reward proactive behaviors. This encourages other workers to speak up about their safety concerns and possible solutions. On-site employees are often the only ones who can report procedures that may be hazardous in certain environments since they have hands-on experience.
Lead by Example
When it comes to handling safety challenges in construction, there’s no better option than leading by example. It’s important that owners wear their PPE whenever they’re on-site, even if they’re just there for a quick walkthrough. Every leader on the field should constantly follow safety protocols to let others know that complacency isn’t tolerated.
Managers can also communicate with workers about the importance of safety protocols. They can share their experiences and act fast to resolve safety problems.
The Major Features of Effective Safety Cultures in Construction
Certain characteristics form part of every successful safety culture. Weaving these elements into your company culture can promote an integral focus on safety at all times:
- Safety-focused leadership: Management should be the number-one resource for safety tips and should hold employees accountable.
- Continuous improvement: Companies should offer employees the opportunity to reevaluate safety procedures.
- Focus on education: Staff should have access to courses to continue learning and meet new industry standards.
- Incident reporting: Companies should put a strong focus on incident reports. They should ensure each report covers the primary cause and action taken.
Actions to Prevent Common Injuries
A few common parts of construction work are responsible for most major and fatal injuries. Here are some actions to implement to reduce risk in these activities:
Working at Height Injuries
Falls are a major concern when working at heights. Below are some essential safety controls:
- Ladders and stepladders should only be used for low-risk, short-duration work.
- If working at a certain height can be avoided, do so.
- Ensure all workers are trained to work at heights.
- All persons working at heights must be supervised by a certified, competent person with the Site Management Safety Training Scheme (SMSTS) or Site Supervisor Safety Training Scheme (SSSTS).
- Ensure the right protective equipment is used.
Slip, Trip, and Fall (STF) Injuries
STF injuries are common in construction, and they can be avoided easily with these practices:
- All staff should wear safety shoes with anti-slip soles and ankle protection.
- Move hazards like trailing cables out of walking routes or put warning signs up.
- Allocate storage areas to prevent materials from piling up.
- Conduct training to spread awareness of the hazards of STF injuries.
Plant Operations/Vehicle Movement Injuries
Workers must monitor vehicles to prevent potentially fatal injuries. Here are some steps to follow:
- Report any equipment faults immediately.
- Quarantine broken vehicles and equipment.
- Construct a traffic management plan that prevents reversing as much as possible.
- Ensure that vehicles aren’t moving within the vicinity of crossing pedestrians or put up signs.
Create a Culture of Safety With The National Association of Safety Professionals (NASP)
If you’re serious about creating a culture of safety in construction, NASP can help. We offer construction safety training specialist courses that meet or exceed OSHA regulations. Our certificates are built for and by safety professionals, and our caring employees always work for our students’ best interests.
NASP is passionate about making the construction industry a safer place to work. We offer site-specific training, consulting services, and classroom training. Feel free to contact us with your questions, or simply click on the course you’re interested in, click “Add to cart,” and go to “Checkout.”