How Can Businesses Eliminate Worker Injuries to Reach a Goal of Zero Incidents?
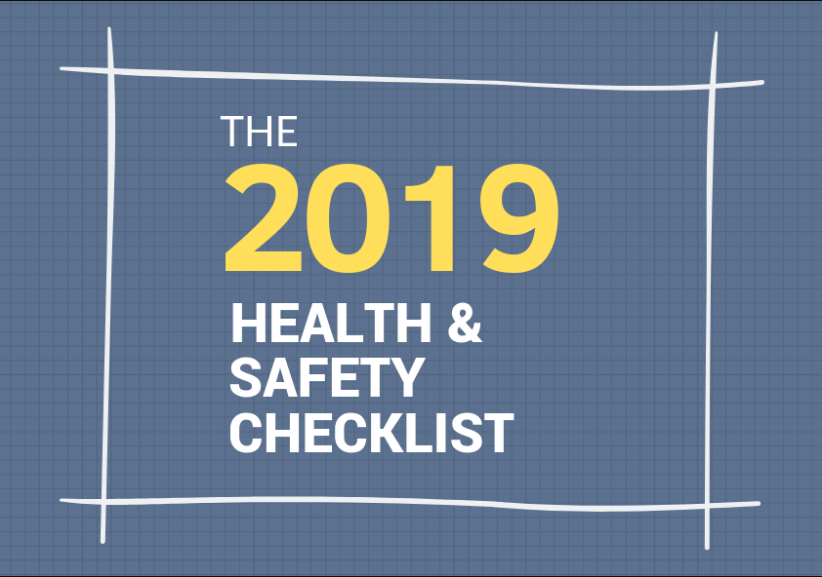
The Zero Incidents Vision
Over the years, businesses have implemented many unique procedures and policies to eliminate worker injuries and workplace incidents. Today, Health & Safety professionals are promoting Zero Incidents as the benchmark for safety management excellence.
A Zero Incidents goal aims to eliminate all events that result in injury, property damage, and have the secondary consequences of:
- Damaging your brand.
- Prompting legal action.
- Halting production.
This Zero Incident philosophy is somewhat polarizing, with some safety professionals who perceive Zero Incidents as the new standard and others who say it is an unrealistic goal. Regardless of whether you’re aiming to reduce your reportable incidents to zero or just reduce your overall incident count, this article will outline some of the fundamental processes that need to be in place to achieve your health and safety goal.
The Journey to Zero Incidents Requires Training
The most proactive way to achieve Zero Incidents is to train your workers—there is a measurable relationship between the amount of pre-emptive training you deliver to employees and the rate of workplace incidences. It’s no secret that staff given proper training about a process and its safety measures are significantly less likely to experience an incident or injury.
However, it’s not enough to simply give good training to your team; these efforts are only effective when you closely monitor employee training performance with the aim to continuously improve the safety record of your organization. Zero Incidents as a target creates the necessity for efforts to establish better management and procedures for training. Being able to create more effective training programs to combat common incidents for your workplace means having an understanding (and way of measuring) both your leading and lagging indicators.
Leading indicators are the measurable factors that contribute to the root cause of an event and can help predict where and when an event is likely to happen – for example, was the employee trained in safe operating procedures, and what safety audits did you do before beginning work? Lagging indicators are the measurable details of an incident that can be observed after the fact, including the type of injury or number of hours of process shut down. Businesses can use lagging indicators to create a baseline to assess management training practices to make improvements. On the other hand, leading indicators focus on future health and safety outcomes with the goal of improving overall safety and reducing injury. Health and safety managers use leading indicators to create new procedures and monitor compliance and lagging indicators to adjust activities and training to avoid injury and reach the goal of lower incidents.
Being able to measure and compare leading and lagging indicators is essential for building a better training program and getting on track to reach a Zero Incidents goal. Some indicators you should monitor include:
- Employees taking training compared against employees involved in incidents.
- Rate of refresher courses versus rate of incidents (per process type).
- Employee wellness programs(for example, ERA provides our staff with an employee gym for physical health and ergonomic sit/stand desks).
- Frequency of safety audits against near misses.
It is important that businesses aim for proper training and fewer incidents without pressuring workers to under report minor injuries. In aiming for fewer incidents, one should also create a workplace culture that is open to (and potentially rewards) reporting from employees rather than an atmosphere of fear and silence. Incentives for training, such as bonuses for employees who participate in safety programs, can promote a no-incident culture by promoting workers who prioritize safety. OSHA’s VPP Guidance materials suggest several positive incentives offering modest rewards for successful company-wide safety and health training. Zero Incidents serves as an opportunity for businesses and employees to learn how to achieve the highest results in workplace safety.
Benefits of Risk Assessments and Root Cause Analysis for Employers
A risk assessment involves the process of evaluating risks to workers’ health and safety from workplace hazards. Risk assessment plans collect vitally important information which can be used to create a no-incidents culture for workers. A proper risk assessment methodology aims to identify:
- Hazards that have the potential to harm any person at a facility. This process, known as hazard identification, consists of recording actual physical hazards that can take any number of forms – from fall hazards, to proximity to dangerous machinery, to injuries from carrying heavy objects, etc.
- The actual level of risk posed to staff and site visitors by any identified hazard, a process commonly referred to as risk analysis.
- Risk evaluation levels or ascertaining the significance of the risk in a broader context.
Health and Safety managers should combine a risk assessment with a root cause analysis to eliminate workplace hazards and achieve low incidents. The Occupation Safety and Health Administration (OSHA) defines a “root cause” as “a fundamental, underlying, system-related reason why an incident occurred, that identifies one or more correctable system failures.” OSHA explains that “by conducting a root cause analysis and addressing root causes, an employer may be able to substantially or completely prevent the same or a similar incident from recurring.” Employers conducting a root cause analysis seek to discover the underlying and systemic causes of an incident that will help prevent similar events from happening again rather than simply correcting the problem itself. In taking actions to identify and correct underlying system management shortfalls, employers can avoid unnecessary fines and litigation.
Interviews, checklists, event trees, and other tools assist employers in identifying root causes for incidents ranging in complexity. A root cause analysis combined with a risk assessment creates a clear, guided course to the goal of less incidents. Employers benefit from reduced failures and prevented incidents resulting in improved process reliability, increased revenues, decreased production costs, lower maintenance costs, and lower insurance premiums.
Conclusion
The most successful improvements in health and safety are based on training and measurements of risk assessments and root causes. Risk assessments and root cause analyses serve to provide “early warnings” about potential hazards to avoid incidents. Once issues in your process are uncovered, training staff on the new procedure is the best way to zero incidents. Zero workplace incidents can be achieved once companies invest time and resources in the right processes.
The aim for zero represents perfection, however employees cannot operate perfectly all the time. Zero is rather a target for employers to demonstrate commitment to reducing workplace incidents to achieve safety for everyone. Employers work alongside employees to reach safety goals; however, employers send the message through company health and safety goals to communicate that incidents are not acceptable. Rather than a numerical goal of zero, Zero Incidents allow companies to show their underlying philosophy—that safety must be emphasized and that human life and injury is of the highest priority.