Identifying workplace hazards
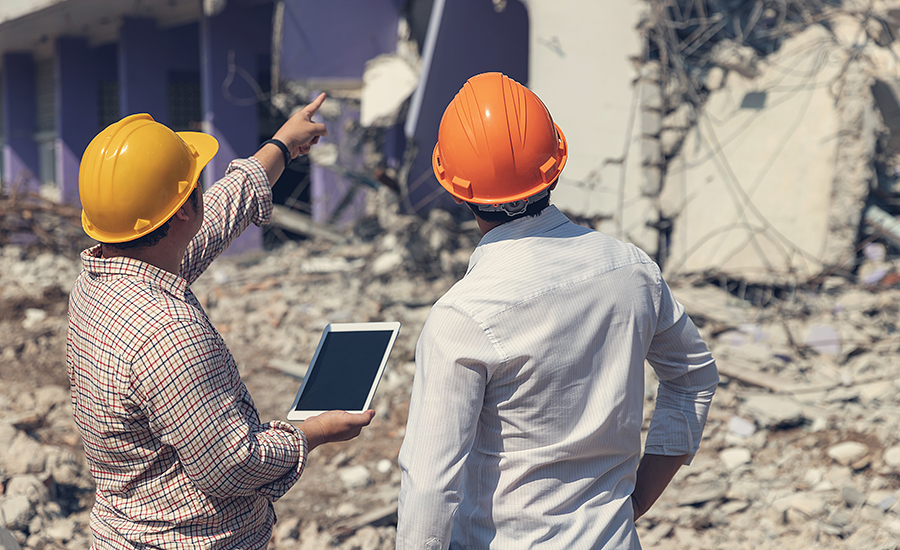
What Methods Really Work?
Seeking safety excellence, we focus on creating a safe working environment by identifying the hazards that exist in our environment — and how we interact with those hazards as individuals.
We proactively seek out what can contribute to an incident and contain, control, or eliminate the hazard before an incident occurs. We also determine where else that hazard exists within our organization and leverage the learning that has occurred and resolve those hazards as well.
Applying the hierarchy of controls provides guidance to how sustainable our actions may be. Taking actions that begin with engineering controls gives us confidence that our actions will provide sustainable solutions.
Visual literacy advances our ability to apply critical thinking by seeing, interpreting, and taking appropriate actions. When we see more, we must also have mechanisms in place to effectively deal with more.
Best Practices
Four mechanisms support our ability to be more successful identifying and resolving hazards that exist in the workplace in a sustainable manner. We begin by developing an inventory of the hazards we identify and determine what risk they represent. Depending on our risk assessment, we contain the hazard until ultimate resolution. We determine where else a similar risk may exist and address it as well. Finally, we communicate what we have found and the action we have taken.
Here’s the challenge: Our work environments are complex and filled with opportunities for something to go wrong. And we often no longer “see” the things around us. They become so familiar they become part of the background and we no longer “see” them for what they are – latent opportunities for something bad to happen. It may be a trip hazard we walk by time and time again, until we don’t. It may be a sharp edge that we negotiate without thinking, until we don’t.
We know our brains determine what it is that we see, and the brain does a lot of filling in the blanks for us. In fact, the brain may fill in as much as 90 percent of what we are looking at based on our experiences, our expectations and our biases. This works pretty well, but not perfectly, when conditions remain the same. But what if conditions change? Will we see it and know what it now means to us?
Hazard Identification Processes
By definition, we are attempting to identify the hazards that exist in our workplace. Common processes can be as simple as hazard hunts and as complex as design for safety reviews. In either case we are dependent on our ability to “see” or recognize a condition as a potential hazard. It is important that these processes begin with objective observation which leads us to whether a hazard exists or not. By improving our ability to make objective observations about the environment and the work activities, we can be more effective assessing whether hazards exist and the potential impact they represent.
By some estimates, up to 90 percent of the sensory information we take in is through the eyes. This is our primary method for understanding the world around us. When we begin our work, we begin with “looking” at what it is we are dealing with. It is by first looking at the task we are about to undertake that we interpret what we must do.
View NASP’s Certified Safety Manager Course
Slow Down to Really “See”
Too often, though, just looking is not sufficient. We must slow down a bit, and move from just looking to truly seeing what is there in order to draw meaning from what we are seeing.
The Toledo Museum of Art’s process “The Art of Seeing Art®” illustrates how we can move from simply “looking” to immediately “interpreting” what we see. When we truly “see” what it is in front of us, we can do a much better job of interpreting what it means.
It is all about what we see, what it means, and what we do about it. Our goal is to see the hazard, interpret it through risk assessment, and take action in response to the risk it represents.
Applying this modification to the Art of Seeing Art® is one way to improve our ability to make the familiar unfamiliar, and begin to see the latent hazards that exist in our work environment or work practices that we have come to accept without critical thought.
We can apply additional tools and techniques such as the Elements of Art (color, line, shape, space and texture) to further de-construct the environment we are looking at. Each element is designed to help avoid our natural tendency to pay attention to some things and ignore others. They also help slow us down and avoid “leaping to a conclusion” that may not be correct.
After Finding Hazard, Take Action
Four mechanisms reinforce an effective hazard identification process after identifying the hazard. They all build effectiveness in resolution and employee engagement.
- Take an Inventory – Conducting a hazard hunt or any form of identifying hazards that exist in the workplace can be a lot of work and needs to be well organized. This is especially true when we apply visual literacy tools and techniques to the process and begin to unearth the hazards that have been in the background and not previously identified.
Catalog the hazards identified, noting their location and with photographs if possible as a solid reminder. Cataloging the hazards ensures they will not be forgotten and provides a metric associated with what has been located.
Use a scoring method to risk-assess the hazards identified so that they can be appropriately prioritized. Hazards that are high risk with imminent danger should result in immediate resolution or stop work. Remaining hazards will need a methodology for prioritization and resolution. - Containment and resolution- Once we identify a hazard through our hazard identification process, how can we contain the hazard until it is resolved? What is the appropriate control to be applied on an interim basis until the hazard is eliminated or the ultimate control is implemented?
Too often we identify a hazard but leave it not contained until we have a solution. In the meantime, we run the risk of the infrequent occurrence of an incident arising although we knew the hazard existed.
The hierarchy of controls highlights the effectiveness of controls. Eliminating a hazard that we have identified through our visual literacy efforts is clearly more effective than just providing PPE to our team members. I have often heard the analogy that PPE and administrative controls are like a block of ice. Solid when first frozen, but without constant reinforcement they melt away over time! - Where else does this condition exist- Once we identify a hazard in one location, it is likely the same hazard or condition exists elsewhere in our organization. We can leverage the learning that occurs in one area and expand its impact to other areas in the organization. The same or similar hazards can be corrected in other locations without the need to re-identify the same condition over and over again. And most importantly, by not experiencing the same incident over and over again.
- Communicate and measure- When we do hazard identification work but don’t communicate about it, we risk our employees will assume the worst – that we did nothing – and will no longer invest their time and effort for something they see no result from.
Communication can be in various forms, including part of the report out in safety huddles, poster sessions, and daily leader communications.
Measurement is also an important. By tracking how many hazards have been identified, we can see trends and celebrate the accomplishments of creating a safe working environment as those hazards are contained and then resolved. Providing visibility through visual communication boards that many organizations maintain on critical performance metrics reinforces the importance of this work and recognize the accomplishments of those involved.
Purchase NASP’s Certified Safety Manager Course